What is Porosity in Welding: Best Practices for Avoiding Permeable Welds
Wiki Article
The Scientific Research Behind Porosity: A Comprehensive Overview for Welders and Fabricators
Understanding the complex systems behind porosity in welding is vital for welders and producers aiming for impressive craftsmanship. As metalworkers delve into the midsts of this phenomenon, they reveal a world controlled by numerous variables that affect the development of these minuscule voids within welds. From the composition of the base materials to the ins and outs of the welding procedure itself, a plethora of variables conspire to either worsen or reduce the visibility of porosity. In this detailed overview, we will certainly decipher the science behind porosity, exploring its impacts on weld quality and introduction advanced techniques for its control. Join us on this journey with the microcosm of welding flaws, where precision meets understanding in the search of perfect welds.Understanding Porosity in Welding
FIRST SENTENCE:
Exam of porosity in welding exposes important insights into the integrity and high quality of the weld joint. Porosity, defined by the existence of cavities or gaps within the weld steel, is an usual worry in welding processes. These gaps, otherwise effectively attended to, can endanger the structural integrity and mechanical residential properties of the weld, resulting in potential failures in the finished product.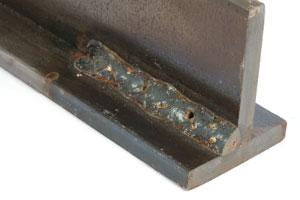
To find and measure porosity, non-destructive testing approaches such as ultrasonic testing or X-ray evaluation are frequently used. These strategies enable the identification of internal flaws without compromising the integrity of the weld. By evaluating the dimension, form, and circulation of porosity within a weld, welders can make enlightened decisions to improve their welding processes and attain sounder weld joints.

Factors Influencing Porosity Development
The incident of porosity in welding is affected by a myriad of aspects, ranging from gas shielding effectiveness to the details of welding criterion settings. Welding specifications, consisting of voltage, existing, travel speed, and electrode kind, likewise impact porosity development. The welding technique utilized, such as gas steel arc welding (GMAW) or protected steel arc welding (SMAW), can influence porosity development due to variations in warm distribution and gas protection - What is Porosity.Impacts of Porosity on Weld Top Quality
Porosity development considerably jeopardizes the structural integrity and mechanical homes of bonded joints. When porosity exists in a weld, it creates spaces or cavities within the material, decreasing the total stamina of the joint. These gaps work as stress and anxiety concentration points, making the weld extra susceptible to fracturing and failure under load. The presence of porosity also deteriorates the weld's resistance to corrosion, as the entraped air or gases within deep spaces can react with the surrounding environment, resulting in degradation with time. Additionally, porosity can prevent the weld's capacity to stand up to pressure or influence, additional jeopardizing the total top quality and integrity of the bonded framework. In critical applications such as aerospace, vehicle, or architectural constructions, where security and durability are critical, the harmful impacts of porosity on weld top quality can have Continue serious repercussions, stressing the importance of reducing porosity through appropriate welding techniques and treatments.Strategies to Decrease Porosity
Additionally, making use of the suitable welding parameters, such as the appropriate voltage, existing, and take a trip rate, is important in stopping porosity. Preserving a constant arc size and angle during welding additionally aids reduce the probability of porosity.
In addition, picking the right securing gas and preserving appropriate gas circulation prices are important in decreasing porosity. Utilizing the proper welding technique, such as back-stepping or employing a weaving motion, can additionally help distribute warmth equally and minimize the possibilities of porosity development. Last but not least, making certain correct air flow in the welding atmosphere to get rid of any type of potential resources of contamination is crucial for attaining porosity-free welds. By applying these techniques, welders can efficiently decrease porosity and produce high-quality welded joints.

Advanced Solutions for Porosity Control
Implementing innovative technologies and innovative techniques plays a pivotal function in achieving remarkable control over porosity in welding processes. In addition, using sophisticated welding methods such as pulsed MIG welding or modified atmosphere welding can additionally aid minimize porosity issues.Another advanced remedy includes the usage of innovative welding tools. As an example, making use of tools with built-in attributes like waveform control and sophisticated power sources can enhance weld high quality and reduce porosity threats. In addition, the execution of automated welding systems with exact control over specifications can significantly lessen porosity defects.
Moreover, including sophisticated tracking and evaluation technologies such as real-time X-ray hop over to here imaging or automated ultrasonic screening can help in discovering porosity early in the welding process, permitting for instant corrective actions. In general, integrating these advanced options can considerably boost porosity control and enhance the general high quality read the full info here of welded parts.
Final Thought
In conclusion, comprehending the scientific research behind porosity in welding is crucial for welders and makers to produce top quality welds - What is Porosity. Advanced solutions for porosity control can additionally boost the welding procedure and ensure a solid and dependable weld.Report this wiki page